Definition of Filtration |
|
Removal of particles from a fluid through a permiable medium or Physical separation of particles through a permiable medium (like Filter cartridge, Filter media.. .etc) |
|
|
|
Need of Filtration Where we required Filtration |
|
|
|
 |
Grinding |
|
 |
Honing |
|
 |
Lapping Cold |
|
 |
Rolling |
|
|
|
 |
Wire Drawing |
|
 |
Components Washing |
|
 |
Gun Drilling |
|
 |
Tool Grinding |
|
|
|
|
Daichi Focus |
|
|
 |
Magnetic Coolant Filters |
|
 |
Gravity Paper Band Filter |
|
 |
Compact Band Filter |
|
 |
ilter Consumables like Filter Cartridges |
|
 |
Non - woven Filter Media, Filter bags |
|
|
|
 |
Centrifuge Oil Cleaner |
|
 |
Magnetic Fine Filtration |
|
 |
Bag Filtration System |
|
 |
Back Flushing System |
|
|
|
|
Magnetic Coolant Filter |
|
|
 |
Permanent Magnet -Ferrite- 3000 Gauss |
|
 |
Rare Earth Magnet- Super Power |
|
 |
Magnet 10,000 Gauss Value |
|
 |
Capacity - 40 to 500 LPM |
|
|
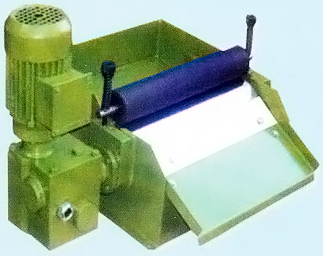 |
|
Compact Band Filtration System |
|
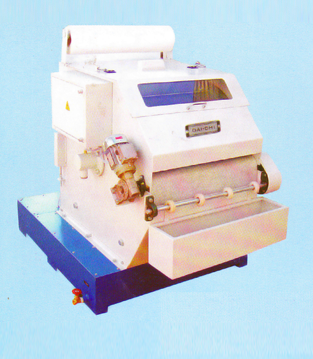 |
Principle of Compact band Filter |
|
Hydrostatic Pressure & Gravity with Zero Leakage in Filtration Chamber due to perfect sealing. |
|
|
|
|
|
Gravity Paperband Filtration System |
|
|
 |
Grinding |
|
 |
Lapping |
|
 |
Cold Rolling |
|
 |
Wire Drawing |
|
 |
Components Washing |
|
 |
Deep Hole Drilling |
|
 |
Gun Drilling |
|
 |
Capacity : 40 LPM to 500 LPM |
|
|
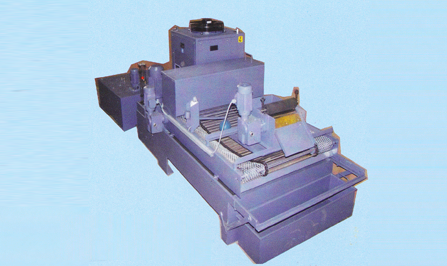 |
|
|
Dai Chi Fine Filtration System |
|
Technology ( Edge Filtration ) |
|
This type of filter element utilizes stacks of paper discs tightly compressed on a tubular core to form a continuous cylindrical surface where contaminants are filtered at the edge of the Filter Candles |
|
Method of operation: |
|
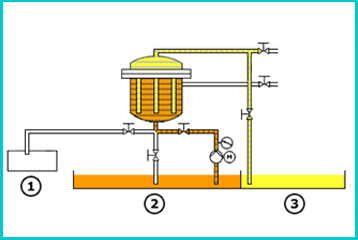 |
|
 |
Sludge box |
|
 |
Fouled tank section |
|
 |
Clean tank section |
|
|
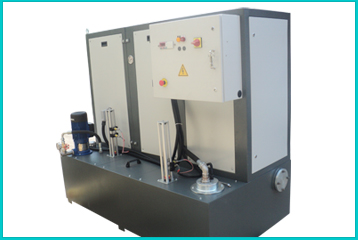 |
|
|
Stages of Operation (Fine Filtration System) |
|
Step 1: Filtering Mode |
|
In normal operation, dirty oil from the Grinding machine is taken from the Dai Chi dirty oil storage area and introduced into the filter vessel. Oil is forced to the center of each element. All particles larger than one micron are trapped on the O.D. of the filter element. Clean oil is then deposited into the DaiChi's clean oil storage area and is delivered to the Grinding machine upon demand. |
|
Step 2: Draining Mode |
|
Prior to backflushing the elements, the filter vessel is drained into the dirty storage area through the use of compressed air. |
|
Step 3: Backflushing Mode |
|
The backflushing mode is fully automated. Compressed air is introduced through the top and center of each element. Dirt and debris are forced out of the filter vessel into the paper lined sludge box, which should be emptied approximately once a month. The entire backflushing procedure takes only six minutes. |
|
|
Advantages: |
|
|
 |
Filtration down to 3 urn below |
|
 |
Automatic operation without the use of consumables |
|
 |
low maintenance cost |
|
 |
Extended Coolant Life |
|
 |
Increase Surface finish of Product |
|
 |
Decrease Production Cylce time |
|
 |
Reduce Operating Cost |
|
|
|
Centrifuge Oil Cleaner |
|
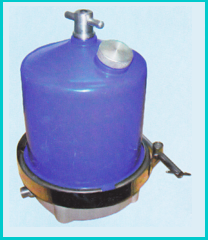 |
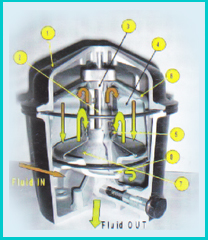 |
|
 |
Body |
|
 |
Spindle |
|
 |
Stand tube |
|
 |
Cleaning chamber |
|
 |
Mesh |
|
 |
Rotor |
|
 |
Drive Chamber |
|
 |
Nozzle |
|
|
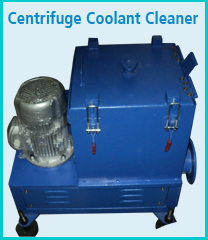 |
|
|
|
Principle of Operation |
|
Centrifuge Oil Cleaner removes very fine dirt from oil up to 5 micron. Inside the centrifuge a twin jet rotor
rotating at high speed up to 7000 rpm, creates centrifugal forces 2000 times greater than gravity. This removes
dirt and contaminants from oil, which is deposited on the inner wall of the rotor as a thick layer. The collected
dirt can be easily cleaned and the unit put back to use again. |
|
|
 |
Industrial Applications |
|
 |
D GSets |
|
 |
Marine Engines |
|
 |
Locomotives |
|
 |
Earth Moving Equipments |
|
 |
Drilling Rigs |
|
|
|
 |
No Replacement Cost |
|
 |
No Recurring Cost |
|
 |
Increase in Coolant life |
|
 |
Finest Filtration up to 5Microns |
|
|
|
|
Filter Consumables |
|
|
|